The resurgence of concrete in staircase design
Thanks for your interest in the Resurgence of Concrete for Staircase Design – we’ve rewritten this information more fully for you here: CONCRETE STAIR DESIGN.
Concrete staircases have a unique design feel all of their own, and the use of concrete in buildings stretches back a long way in our history – the ancient Romans used an early form of concrete and were skilled exponents in this kind of building technology. They developed forms and moulds which allowed them to produce concrete in many different shapes and sizes. Across Europe, they used precast concrete in buildings, bridges and aqueducts for more than 200 years. Precast concrete then largely fell out of use in Europe until it was rediscovered by builders and architects in the late 18th century.
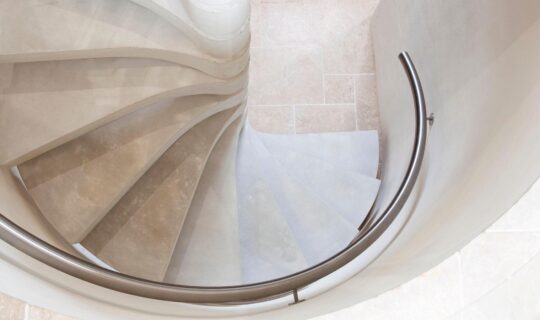
A resurgence of interest in the use of concrete finishes for home interiors has led to concrete staircases increasing in popularity. This is due to their versatile nature allowing for extremely stylish and contemporary looks.
Concrete can suit a variety of staircase designs and is commonly used for treads on spiral stairs, straight flight spine beam stairs and in floating or cantilever stair designs. They tend to be either created on site where the treads are poured in situ or precast in a factory and installed on site.
The practical benefits of concrete as a material in stair design
There are a number of practical reasons why we are finding contractors and homeowners are turning to concrete stairs as an interior design option.
- Due to the low cost of the raw materials, they are relatively economical to produce and minerals can often be sourced locally.
- They are very robust, durable
- They will not rot, fade or warp over time
- They are easy to maintain and long lasting and if they do require repair, for instance due to impact damage, this is normally a straight forward process.
- Concrete is inherently resistant to fire and therefore can help to enhance fire safety in a building
- Concrete stairs are quiet as they do not create creaks or echoes
- They can help to improve sound-proofing between floors in a building
We believe modern technology has also enabled the creation of some beautiful concrete stair designs.
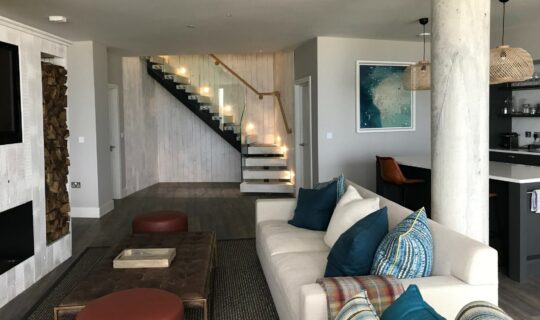
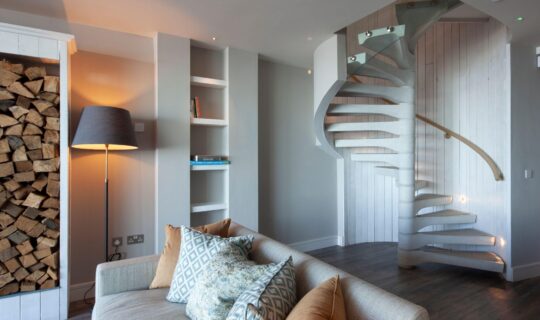
Enhancing the ever-important interior design statement
Concrete spiral stairs can make a brilliant architectural statement within a building, creating a real centrepiece and focal point. Furthermore, concrete helps to create an imposing sense of solidity and permanence to any building.
Because concrete is a fluid material, it can be poured into virtually any shape. It can also give a very smooth finish that is free of any defects or flaws. This allows for the creation of some arresting and stylish concrete staircase designs with impressive geometric shapes that can be used to form a stunning, contemporary design feature.
Advances in production technology and computer design have added further momentum to this trend for imaginatively designed concrete staircases. Now it is possible to produce cantilever or floating stairs in concrete, which can make also make a striking staircase.
While the natural look of concrete can be very beautiful, concrete stairs also provide a solid base for many other types of finish, such as stone, timber, marble, tiles or carpet inlays. The concrete itself can be given a colour tint or finished with a textured surface or pattern. All these options help to give the customer great scope when specifying their bespoke concrete staircase.
When paired with other materials for the balustrade and handrail concrete stairs can also make a good design feature. For example, the combination of concrete stairs with glass balustrade can create a sleek, stylish and modern look. The use of recessed lighting in these staircases can further enhance this effect.
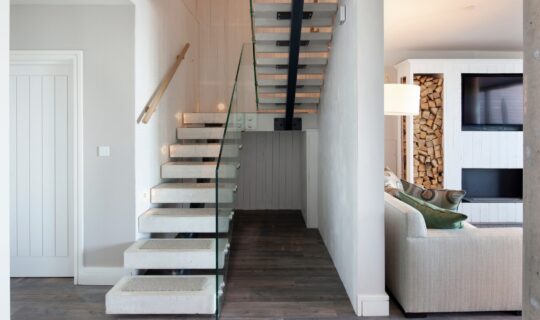
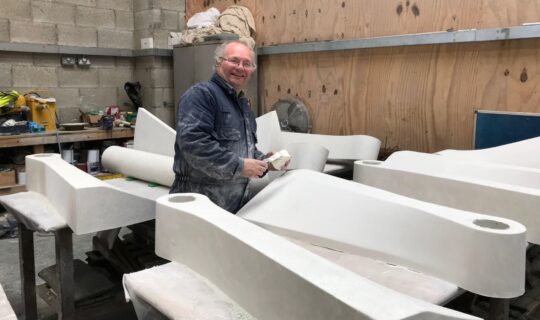
The manufacture and install process for concrete stairs
Most of the concrete staircases that Spiral UK produce are installed using pre-cast treads made in house. The moulds for these are created in fibre glass with the concrete mixed in the factory and then poured into the mould over reinforced caged steel. We do pour at site if required but we prefer to create pre-cast treads, where we can, so we can manage the curing process.
Standard mixes are tested every 6 months for strength and colour testing can be done using samples and different volumes of pigment to colour match. Different types of aggregate and sand can also be used to give a different surface finish.
A white fair face trowel finish is currently the most popular, but it is also possible to create an exposed pebble dash finish too.
All pre-cast treads are sealed with a silicone- based sealant to protect and prolong the life of the stair.
When installing a concrete staircase near a swimming pool the reinforced steel cage will be galvanised to prevent rust from the chlorine present nearby.
Final finish will depend on the environment and purpose of the stair. Depending on how many people are using the stair it may require nosing to be added to the tread or trace heating may be required externally to prevent ice forming.
The challenge with concrete production is temperature a colder environment means the concrete takes longer to cure so it’s important to keep the temperature consistent to maintain cure time.
It’s great to see concrete staircases contribute so beautifully to the interior design of a property adding to a light airy space or blending seamlessly with a clean, modern look and feel. Long may this resurgence continue.
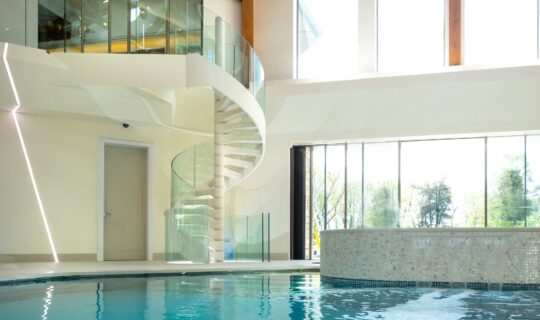
Eric Nicholls is the Managing Director of Spiral UK. He has been involved in the manufacture of bespoke staircases since starting the business in 1985. Eric is a BSI Committee Member and Chair of the Cornwall Manufacturers Group.
For more information on concrete staircase design see our concrete staircase section.
If you’d like to discuss a staircase design with us please get in touch.